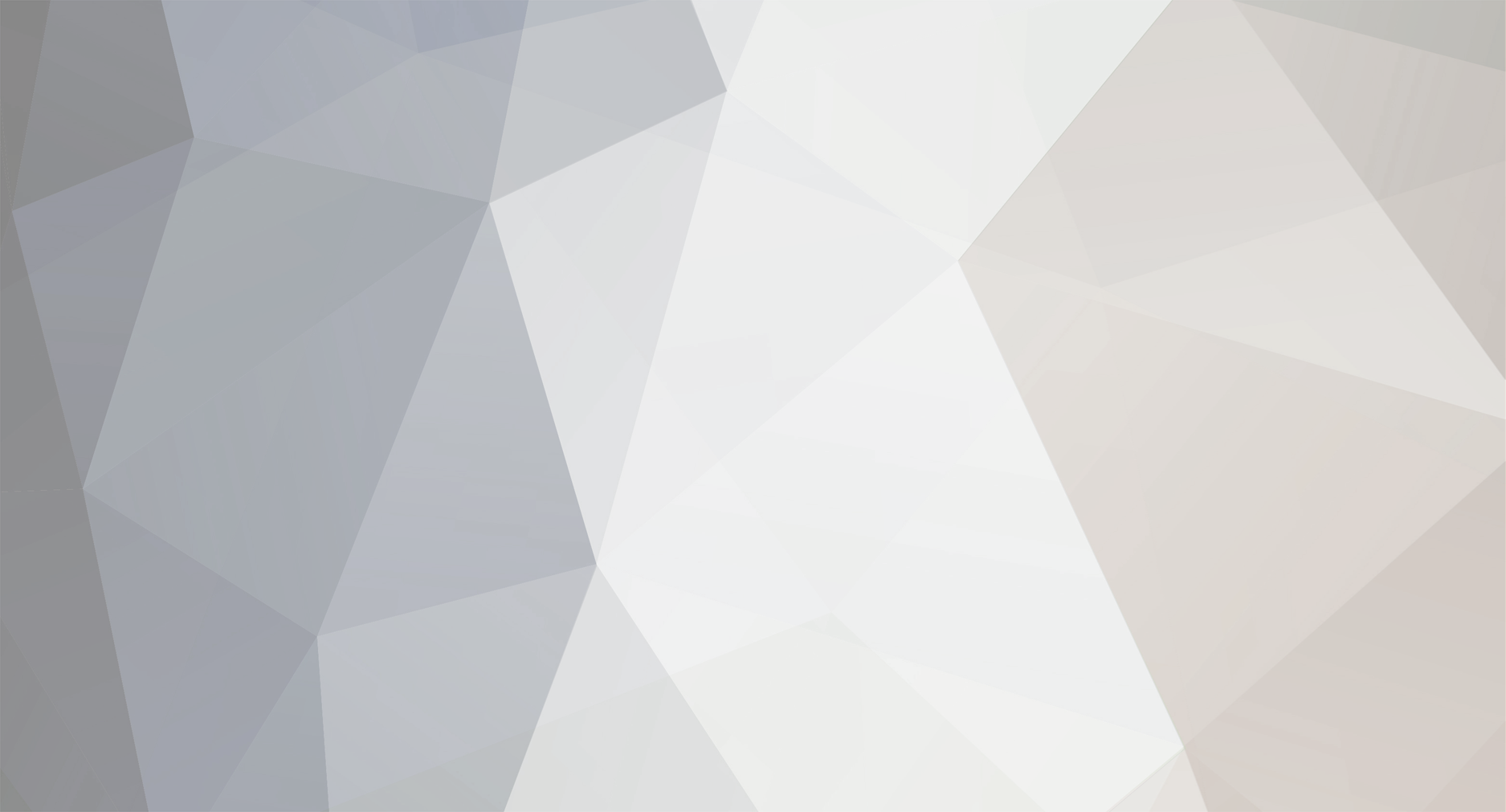
Mech
Premium Members-
Posts
3,946 -
Joined
-
Last visited
-
Days Won
264
Content Type
Profiles
Forum
Gallery
ATV Magazine
Events Calendar
Downloads
Store
Community Map
Everything posted by Mech
-
Too bad you threw the original away because it looks like it just needed a clean. Any after market carb might be just as problematic as the one you already have. Did your new carb come with any spare jets ? They sometimes do. Since it idled ok, and I'm presuming from your description that you weren't giving it full throttle, the problem perhaps lays in the 1/4 to 7/8 throttle opening systems of the carb ? That range is cobntrolled by the slide and needle, and the discharge tube the needle slides down into. You could try changing the height of the slide needle in the slide. There's a clip on the needle and if you raise the clip up a groove in the needle it makes it run leaner between 1/4 and about 7/8 throttle, and if you lower the clip it makes it run richer. You can try raising or lowering the clip and as long as you note where it was originally, and whether it runs better or worse in that throttle range after the change, then you will have an idea about whether to move it further or back the other way by two notches. That's an easy job to do in place, and easily undone. Since you thiink it was sloping ground that made it run bad, as opposed to the load being put on the engine, perhaps it needs the float level adjusting as well or instead of the slide needle adjustment. That's a bit trickier to do, and undo, but you could test the theory by accelerating along the flat, accelerating up hill, and accelerating down hill. If it goes real bad uphill but it's ok on the flat, that would sort of indicate a bad float, but you need to be putting similar load on the engine in both cases to really get a feel for it. You could also try just riding along nice and gentle with hardly any throttle seeing if the engine surges or falters going on the flat or up hill. If it runs a lot different going up a hill, than it does when under power and accelerating on the flat, it might point to the float level as well.. If you read the manual, it may be that that bike's float level can be checked with the carb still on the bike. They might use a clear plastic hose to gauge the fuel level in the carb.
- 11 replies
-
- carb
- big bear 400
-
(and 1 more)
Tagged with:
-
ok. Then I think this will be the electrical section for your bike, from the yamaha manual.. Doesn't look to be much different, but.. I still think you should check there is power coming out of the stator's cdi windings, and that it's getting to the cdi. If there is power from the stator to the cdi, then I'd disconnect the kill wire at the cdi and try it. output.pdf
-
I'd check the flow through the carb too..
-
Yup, the petcock is the fuel tap.
-
Does your cdi have three pigtails with round plugs, or two rectangular plugs right on the cdi body ?
-
You've already checked the stator's cdi windings resistance.. what you need to do now is check they are putting out some power..
-
Either a shortage of fuel from the tap, or some electrical component is getting hot and temporarily closing down. If the tap's not letting out enough fuel to keep up with the requirement when the throttle's open, or the float needle's partly blocked causing the same problem, then it can take quite a distance before the shortfall shows up. If you turn the tap on and open the carb drain screw it should be obvious if it's not maintaining flow. Make sure you watch it for long enough for the bowl to empty and then see what the flow's like. The electrical's a bit harder to diagnose but if you have a timing light you could drive down the road watching that to see if the spark fails after a while, or take a spark-plug with you and quickly connect it to the lead and check for spark when it stops running.
-
The readings and behaviour you are getting from the orange wire to the coil, that would be consistent with a trigger coil letting the cdi discharge all the time, so the capacitor never built up to a high voltage. That could be caused by a backwards(for the cdi) trigger winding. The other thing you get is that the cdi expects to get a certain number of AC waves, both/either to build up a high enough voltage or as part of the timing, and/or if the windings start on a positive wave after a trigger and discharge, when they should be starting out with a negative wave, then they miss some waves getting rectified into the capacitor and it gives a weak discharge on the orange wire. There are several problems if we put the wrong cdi onto a stator not designed for it, or a bike with the wrong stator for the wiring and cdi, but some of them we can fix by experimenting swapping the two cdi charge and the two cdi trigger wires. Oh, and they send a start signal to the cdi, and some models send a voltage into the cdi when the start button's pressed, and other models run power through the cdi to the start button and then detect the voltage drop when the buttons pressed.. You really need the right wiring diagram and resistance figures. I'd try that before fitting a new stator, which might not suit the bike or the cdi and so complicate things even more. If you give us all the details you can about the bike, including the numbers of course, and tell us what coloured wires are going into what shaped and coloured plugs at both the cdi and the stator, I or someone might be able to find you the wiring diagram.
-
And non genuine cdi are a bit of a gamble about it being the right one for the bike.. They make a lot of models of cdi to match a lot of model bikes, and they rewire the cdi charge, and trigger windings, so they don't always work with a different version with same numbers of wires, or plugs, or colours of plugs. Sometimes swapping the two charge wires about, and/or the two trigger wires about, which requires a total of four different ways of connecting those two sets of wires to have tried all options, sometimes that gets a wrong model cdi going. Sometimes though the resistance readings of the stator and trigger are different and put out more or less power and sometimes it doesn't work, or perhaps works briefly before something fries.. haha.
-
#2 "Then you should check that the windings are putting out some power, because sometimes the magnets drop off or get shorted by metal dust and even though the resistances are ok, they don't put out power."...
-
We don't know that the second hand cdi is "a known good unit", to use the manual's phrase.
-
Well my first thought was that the brakes were locked up, but you are quite certain that the diff and axle turns when the drive shaft's disconnected, but locks up when the driveshafts on.. right ? So, if you disconnect the driveshaft from the diff, does the driveshaft turn the engine's output shaft ?
-
It's sometimes possible to remove the tensioner, drop the cam sprocket off the cam, let the chain off so there's more slack, then try to get the chain to go back on the bottom sprocket by manipulating the chain, possibly with a length of stiff wire down the hole levering the chain over. Then put the chain on the top sprocket, lift it onto the cam shaft but don't put the bolts in, check and redo the cam timing being careful not to bend any valves, then assemble it back up. If you can't get the chain on the bottom sprocket then yeah, you take the side case off again. Stateing the obvious perhaps, but, you have to check the cam timing with the slack taken out of the chain and all on the tensioner side. I'm not sure how much travel the tensioner should have, but it needs to be enough to take the slack out of the chain. It would be a good idea to figure out why the chain slipped. The tensioner has a ratchet mechanism, visually check the teeth and pawl of that, and test it lightly, with big pliers perhaps, but only gently.. The other thing that happens is that people don't get the two slippers sitting in the correct places at the bottom, or even up the top on some models. If/when everything looks and tests ok then put the tensioner back in and turn it over..
-
It needs a better spark to jump under compression than it does at atmospheric pressure. A new spark plug might fix it, or the coil or plug lead/cap might be defective and letting the spark jump out of the engine, but once in and under compression the spark might find it easier to jump to earth through some bad insulation or an internal short in the coil. Most coils they say to test by making sure they will jump a spark six mill which is 1/4 inch. If it will spark that far then it's internal insulation is good, but the cap or wire could still short.
-
Check the resistance of the two ignition windings in the stator that are to charge and trigger the cdi. If the resistances are ok then replug that connection and go to the cdi and check the resistances of the two same windings and wires on the pins in the plug there, that confirms the wires are ok. The resistance readings should be very close to the readings down at the engine/stator. Then you should check that the windings are putting out some power, because sometimes the magnets drop off or get shorted by metal dust and even though the resistances are ok, they don't put out power. The winding that's to charge the cdi will put out an AC current, and the trigger coil will put out one pulse/wave of current per revolution. To detect the trigger it's best to use an analogue gauge because you'll see the needle flicker but digital gauges miss a short pulse often. The orange wire from the cdi doesn't have power in it till the cdi fires, then it has hundreds of volts and huge current, so you shouldn't put your gauge on it.
-
All good. Have fun.
-
There's a lot needs explaining .. Apart from my questions in #3, did it stop unexpectedly or did it get turned off ? When it first wouldn't start, was that because the starter wouldn't crank or because it wouldn't run when cranked? Which came first, no start or broken bolts ? At this stage it's possible the flywheel key is broken, and that that was the original problem, or a subsequent problem. The sprocket and chain look good, I doubt it's jumping if the tensioner is working.
-
It can't rev if no air is getting in, so, yup, check the throttle cable first, that's the most likely, then check the butterfly is actually closed off and not either bent or being held open by the idle speed screw. If the throttle/butterfly is closed then check the inlet manifold isn't leaking.
-
I'd try and figure why the three bolts broke, and what that might have damaged.
-
Ha yeah that's what I was thinking. You're going to get it going and be looking for something to mow. You might just have to think up reasons to drive it around... To the store maybe.
-
Did you change the cam timing when you replaced the starter clutch ? And are you saying the cam timing is changing from where you had set it to ? And what's the play in the crank ? What direction is this play ? The starter clutch shouldn't effect end float or rotational play in/of the crank.
-
Very good. Hope you're letting the grass grow.. ready for it.
-
Gee.. And I thought honda designed things nicely. Perhaps your hands are too big ? I'm fairly small and my hands only just squeeze in some places. I could see someone with big hands finding a lot of jap stuff a bit cramped.
-
Yeah I can't think of any way the sprag could damage the gears though, not without over revving the starter motor. I think the gear problem was the starter only working on half the gear width. There are sprags in car starters and they sometimes make a bit of noise on the over-run but be fine. And they have sprags in auto trans and they get filled with clutch plate and metal sometimes, but clean out and pass inspection to be used again.. They are super reliable things.