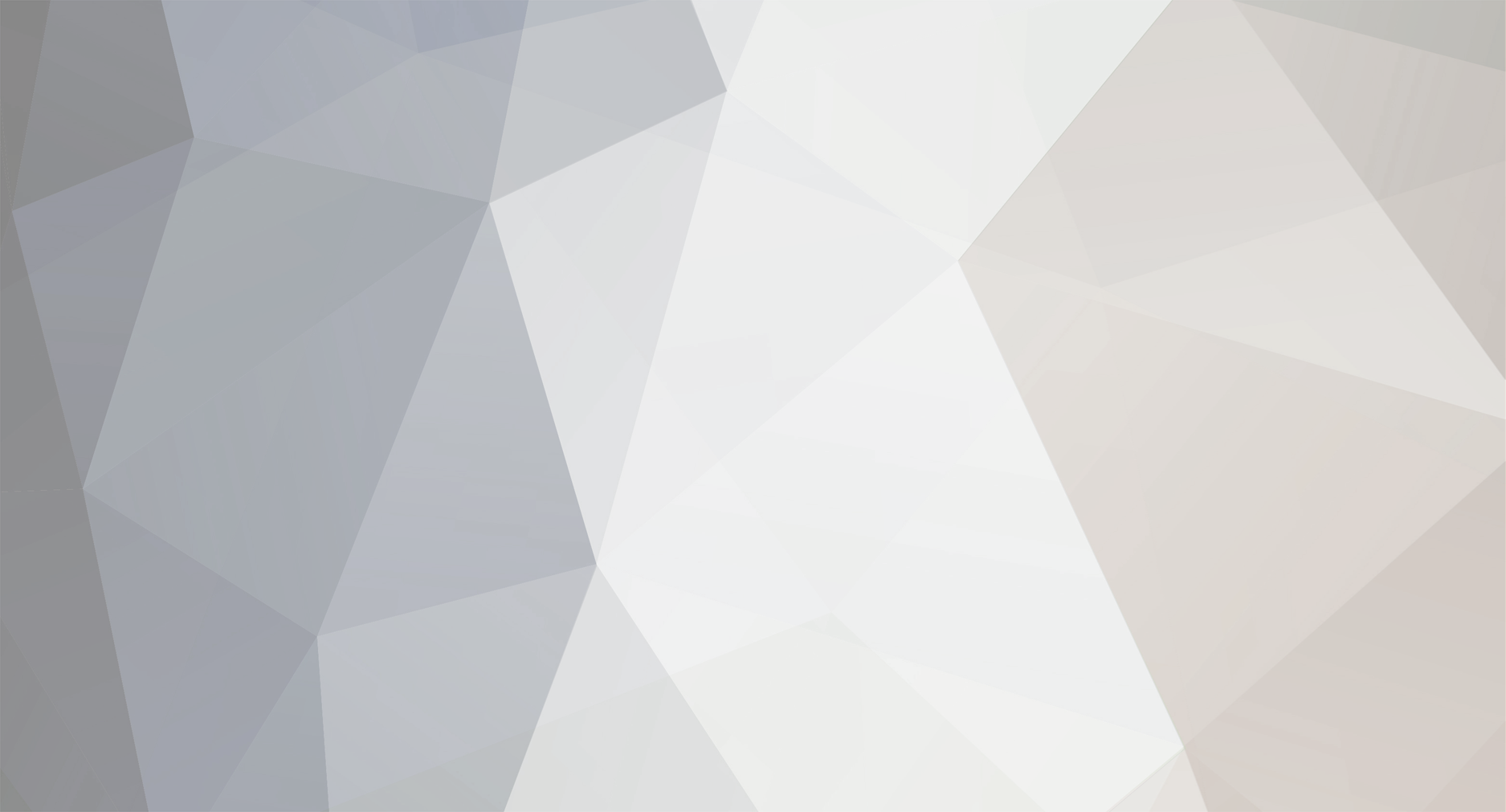
Mech
Premium Members-
Posts
3,955 -
Joined
-
Last visited
-
Days Won
264
Content Type
Profiles
Forum
Gallery
ATV Magazine
Events Calendar
Downloads
Store
Community Map
Everything posted by Mech
-
You should take Gw's advice and lap the new valves in. You should fit new valve seals too. I'd have tried lapping the old valves in if it was me. They clean up mostly if it's only a bit of rust on there. If a motor's burnt a valve or distorted one then they might need cutting, but mostly we can get even those valves to lap in. Valves these days are tough ! And some valves cost a lot more than a seat and/or valve cut. If the seats won't lap to a nice even line, that's not too thin, without rust marks across them, then the seats will need cutting. And after cutting.. you lap them in.. always.
-
I'm pretty sure the pressure should be more like fifty pounds.. I'd let it run pumping fuel.. I've looked in the books before trying to figure how the ecu knows to switch the pump off and there doesn't seem to be any pressure sensor. So.. either the pump runs full time, (and it is possible the ecu would slow it at low fuel requirement times), or, it detects the load on the motor when the pressure gets high and switches off. If the new motor was a bit tight or drawing too much power it might be tricking the ecu.. A few minutes run might get it drawing less amps.
-
Yup, if it's just saving legwork then a quad is cheaper and simpler to maintain. They aren't really safe though on hills towing a trailer. Having the load on the back if you are carting something on hilly land, is better than towing a trailer... Better traction, safer. I manage to get most things I want to move on my quad somehow.. I've used wooden outriggers to lug 14 foot slabs of 3x18 inch, and have a bin front and rear that carry a lot of small stuff or loads of metal or shale.
-
Have you tested the pressure right at the tank or pump, or without any regulator ? It might get better if you let it run free for a bit, pumping fuel through.. You might hear the revs increase after thirty seconds free run..
-
Low voltage to the pump... Bad earth at the pump...
-
Lol.. Life's good.
-
That's a fair deal... I'd get it in writing...
-
To start it needs the neutral light on, and the key, and the kill on. They also start(for future reference) in gear, if you apply either brake hard enough to get the brake light on. Since it's not starting you need to check whether the power is getting down to the starter solenoid on the small wire when you push the starter button. If it's getting there, check the solenoids other small wire is making a good earth and take not whether the solenoid clicks or shows any signs of life, such as buzzing or vibrating. You could also use a jumper from one big solenoid terminal to the other and check the starter does spin the engine over. That checks the starter motor. If there is no power getting down to the solenoid you need to check why. Check the starter button is getting power to it when the key and kill switches are on. Get a service manual and follow the wire diagram back from the starter solenoid's small wire to the start button and then on to where it gets it's power from. The starter button may have dirty contacts if it's sat out in the weather unused for a long time.
-
How ? By rocking it and moving the gear change shaft repeatedly ?
-
Are low idles bad opinions and facts - Suzuki lt185
Mech replied to Powersrepair's topic in Suzuki ATV Forum
Yeah the emulsion tube can be a bit stuck. It will tap out from the top though. I always use a small screwdriver upside down, so the plastic handle hit's the emulsion tube. And that pilot jet Gw is mentioning is the idle mixture screw.. right Gw ? Yup, that should be taken out, along with every other brass jet in the bowl. The air jets near the air cleaner side can be left in but blown through. You need to blow through every jet, and look through them. Sometimes they blow through but when you look you notice they don't look quite perfectly round and clean.. If they don't look perfect, sharpen a small piece of hard wood to a fine point and ream the jets with that gently, gently so you don't break the wood off in the hole.. haha. The emulsion tube has tiny holes up the side of it, several of them, they all need to be clean. They are too tiny for a piece of wood so a wire from a wire brush is a good thing to poke through them. Clean the drilling the emulsion tube fits into. Blow through all the drillings in the carb body. Check how the float needle seat seals. It may have an O ring that needs replacing. Check the rubber diaphragm on the slide for splits. You need to stretch that to find splits sometimes. When you put it together, before fitting the bowl, tilt the carb so the float is hanging away from the needle, then blow through to fuel inlet while you slowly tilt the carb so the float swings against the needle. The flow should stop completely when the float seam or flat surface, or the metal plate that's a part of the float, comes parallel with the bowl's mating surface. When you put it back on, and are sure it's completely clean, if it runs bad between a quarter and three quarter throttle, try moving the slide needle. It generally needs the clip moving down on the needle, which raises the needle and richens the fuel. That's generally what they need. If it's lean it will tend to backfire out the inlet, and/or, die out. If it's too rich it will mostly run ok but be down on power and sound chuggy(if that's a word). .. -
Are low idles bad opinions and facts - Suzuki lt185
Mech replied to Powersrepair's topic in Suzuki ATV Forum
At that throttle setting it will probably be the emulsifier tube or the drilling it is in is dirty, or, the slide needle needs adjusting, or, less likely, the main jet is really dirty.. But before you change anything you should use the drain screw on the bottom of the carby and check the fuel is getting into the carb at a good rate. If it runs for a few seconds then starts to slow, with the fuel tap on, then the float needle system is blocked or needs adjusting. -
700 cc dinli atv mixing water to oil
Mech replied to Shadow1's topic in General Talk - Anything Goes!
You should check it first.. Look for small bubbles in the top of the radiator or the overflow bottle. There could be wear on the waterpump shaft causing water in the oil, or corrosion somewhere near a gasket or O ring, corrosion in a frost plug in the engine somewhere, a crack somewhere. Most of those won't make bubbles in the coolant. -
700 cc dinli atv mixing water to oil
Mech replied to Shadow1's topic in General Talk - Anything Goes!
A blown head gasket can cause it... -
CDI replacement for 1986 Yamaha yfm80
Mech replied to M4ATVfun's topic in General Talk - Anything Goes!
We'll keep our fingers crossed.. -
CDI replacement for 1986 Yamaha yfm80
Mech replied to M4ATVfun's topic in General Talk - Anything Goes!
Could have the flywheel off the wrong model bike on there.. they make a heap of different configurations of magnets and keyways and triggers.. -
It sounds like it is stuck in gear then. It might be in the shift mechanism which is in the side case on the motor. Some bikes the side case comes off with the engine in place..
-
Does it feel like it's changing gears ? Do the grips move a suitable distance when you rock the bike ? You say the bike tries to move when you turn it on, is that at an idle or only when you rev it up ? Do you know whether this thing has an auto clutch ? It may be as the old owner says and stuck in third.. If you pull the side cover to replace that shift shaft then you will be able to operate the linkages inside and tell whether it's stuck in third, or whether it's just the linkages and shift mechanism not working. I'd do that before spending much money on the small stuff.
-
CDI replacement for 1986 Yamaha yfm80
Mech replied to M4ATVfun's topic in General Talk - Anything Goes!
There will be plenty that would work if you are willing to modify the wiring like that... There will be plenty too that won't work. Are you sure that timing isn't because the flywheel key has sheared ? If the trigger coil is mounted too close too they also get a bit advanced, but not generally that much. If it's still got a good spark I'd be checking in the flywheel. Someone might have moved the charge coils, key's broken, trigger coils mounted too close or in the wrong place... Maybe. Some parts places have a feature where if you look up a part, they will tell you what other models that part fits. You might be able to use a genuine cdi off a later model, or, find an aftermarket part that fits that later model the parts list says is compatible... -
It must of been an unusually bad one. Most of the aftermarket carbs I've seen have been ok made, but not tuned for any particular bike or market, and so needed retuning. They generally run after a fashion though, and don't have that problem. And nope, I don't know where to get parts.. I'm in New Zealand.. We just fix everything with number eight fencing wire.
-
I thought that had an auto/centrifugal clutch, so no clutch lever or cable... To get it out of gear you might have to rock the bike back and forwards while you are trying to move the gear change stub.. Really though to fix that gear change properly you really need a new change shaft and lever. To get the change shaft in will require taking the side cover off so you'll see if there is a problem with the change mechanism once you are in there. Always best though to try and get them rideable before making the final list and committing to repairing them, so you don't spend money of it before finding the motor or the transmission's buggered..
-
Oh yeah get the filter on there.. That might cure it. They might have warmed the bike up before you arrived to cover up a few small faults.. The carb should have a strong return spring inside that cover.. Perhaps the throttle cable is old and wasn't returning properly.. You should check the kill switch works !!
-
If there's a stub of shaft poking out of the engine then try gripping it with slipjoint pliers and changing gears. The suspension might have worn ball joints, or bushes, or, the bolts that go through the bushes might be worn in their holes in the chassis.. The lights might just need a new bulb.. or wiring repaired.. The Universal joints.. It's all pretty simple to get them apart. You take the circlips out/off and then rest one yoke across the open jaws of a vice, then hit the other yoke downwards to drive one cap half out, then flip it and repeat the process with the other cap. Then use pliers to pull those two caps right out. One yoke will come off then. Then you rest the bare crosses shafts on the vice and do it again with the other two caps. To get them back together you clean up inside the yokes with emery tape and give them a grease. You take all four caps off the new cross and make sure they are full of thick grease and use a finger to spin around inside there checking all the little needles are sitting nicely. Inspect the cross. If it has a grease nipple in it's center, then there will be one yoke with longer arms to give clearance for the grease nipple. You have to fit the cross the right way over if that's the case. Leave the grease nipple out for now, Then work the cross into one yoke and poke one end out of the hole in the yoke as far as possible, fit a cap carefully on there making sure you don't dislodge a roller. Now keeping the cross into the cap so no roller can get dislodged, tap that cap right in, and use a socket to tap it through more than needed so the other end of the cross is poking out far enough that you can fit another cap, again fitting it carefully so no needles get dislodged. While you are tapping that first cap and cross through you need to hold the cross backwards so it stays in the cap. That requires holding the yoke and the cross in one hand while keeping a bit of pressure on but it's pretty simple. Then tap that second cap into it's hole pushing the cross and both caps into the center. Fit the circlips to those two and then repeat the process with the other yoke and two caps. The danger is dislodging a roller, but that can't happen as long as you keep the cross fully into the caps as you work. You push the cross in and through too far so you can get the second cap on fully without needing to pull the cross out at all. The whole secret to doing it successfully is in pushing the first cap way through the yoke before fitting the second cap on. Sometimes they need pushing through until they are almost coming out inside the yoke, but most bike uj have a bit of recess that means that's not necessary. Take care no to push the first cap right through or it is hard to get back into the yoke. There's a bit of leeway.. You'll see. It's simpler to fit the cross to the long shaft first, they you only have to hold and manage a short yoke for the second set of caps. It's not essential, but after it's all together with the circlips in/on, hold the long shaft and tap on the sides of both yokes and wriggle the cross around a bit to settle things into place and centralise them. The cross should feel free and smooth to move, if it isn't, tap it some more.. You should download a service manual, it will be helpful for the wiring issues if nothing else.