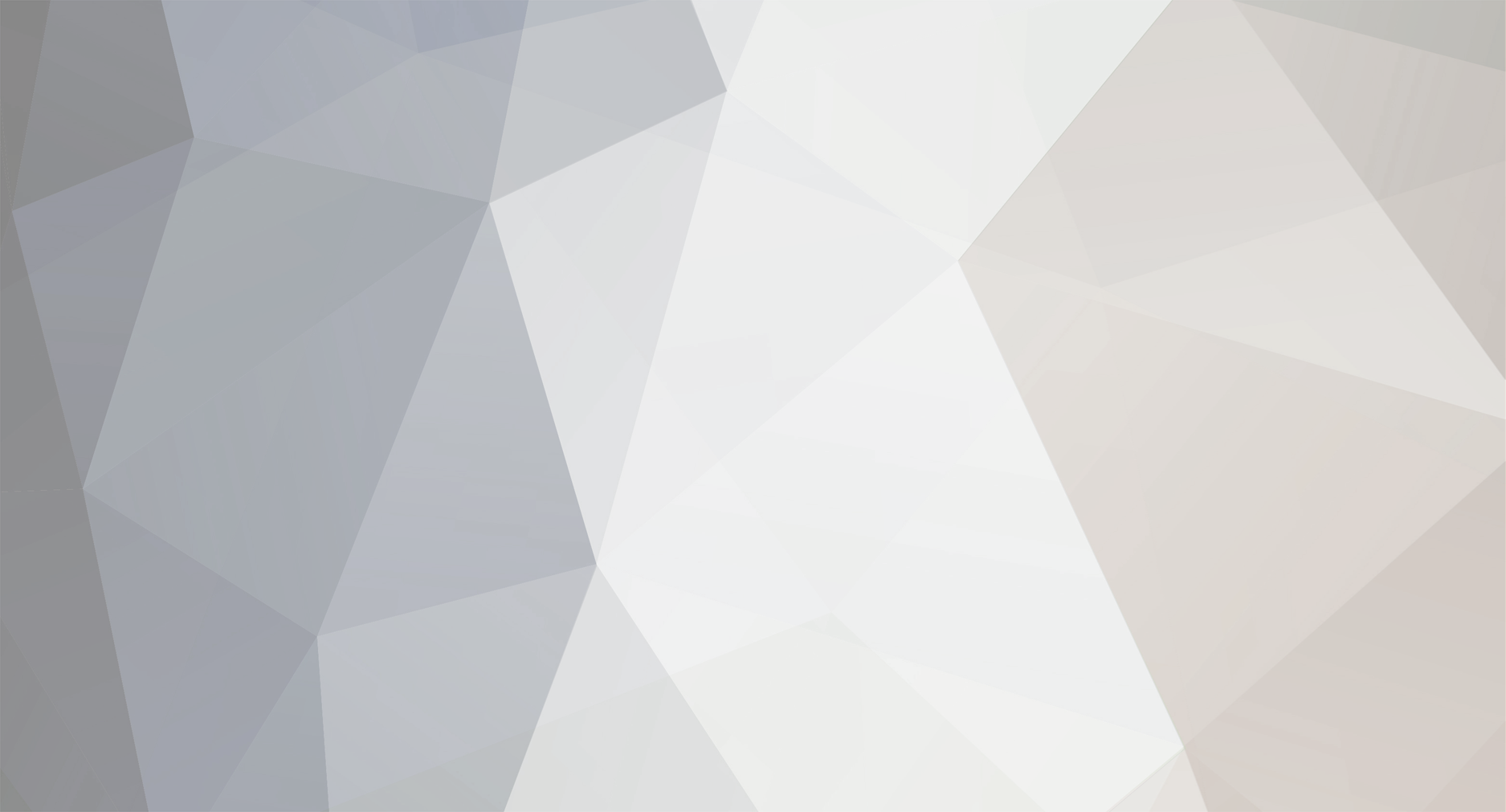
Mech
Premium Members-
Posts
3,955 -
Joined
-
Last visited
-
Days Won
264
Content Type
Profiles
Forum
Gallery
ATV Magazine
Events Calendar
Downloads
Store
Community Map
Everything posted by Mech
-
Try these guys.. They used to have an amazing range of old OEM parts... https://www.anacondaltd.co.nz/
-
The high speed mixture is changed by moving the slide needle or changing jets. There will be an idle mixture adjustment somewhere though, perhaps underneath at the front/engine side and facing downwards. Aftermarket carbies often need some adjusting to get them to run right.
-
Yeah well I'm a mechanic and I manage to overhaul things for an economical price for people.. My customers don't think it's a waste.. I don't like the idea of scrapping things just to go buy a new one..
-
The gearboxes are simple too.. Most manufacturers design their gearboxes these days so it's almost impossible to get them wrong. All specialists tell people that they need their help, and that there are dangers involved, and that paying more and getting them to double up on things is the premium way of doing it.. There is a lot of bullshit and pandering to people's vanity involved in a lot of it... I've seen it and been inside it.. It's why I became self employed.. I always advocate that people should have a go at fixing things themselves. I've always been willing and happy to give my time to anyone that wanted to have a go themselves. In the mechanical field, there's nothing that somebody else can do that we can't do with training and care.
-
Wheels hit solid things all the time.. I think Vince is having you on. If a gear broke and the gearbox locked up maybe.. but a wheel.. Pffff.. Anyway, when I was young and not very careful I put a crank together and didn't align it carefully enough... you know what happened.. It vibrated for about three seconds then started to get smoother and smoother.. My sons have done the same.. After a few revs they are as good as gold.. and go for years.. Weird aye ? But then I wouldn't have been building race engines like you.. I just overhaul them. About the minimum you need to do one is some way of pressing them apart, I use a thick disk of steel with a slot in it, and a hydraulic puller, then V blocks or a set of centers, and some sort of dial gauge that reads thou.. A bit of angle iron to align them as you start to press the second half on and then learning how hard to tap them to align them.. basic hand skills. Seriously, a kid can do it..
-
" If there is any slop there the motor is junk. You'd have to split the case and send the crank off to be split and new rod installed and welded. It's not worth it.". They aren't that bad.. The rod kit is often about the same price as a piston, and they are easy to rebuild, it doesn't take much at all, a set of centers is the main thing, to align the crank when you assemble it. My sons used to overhaul cranks by themselves when they were thirteen, using my vices to press them because they found it too awkward to hold the puller, and pressing plate, all at the same time.. They broke two of my vices doing that.. little buggers.
-
I'd check the engine, frame and the negative terminal of the battery are all properly connected by their respective earth wires.
-
Grizzly 700FI EPS, Intermittent Hard Start, EPS Light on, Codes 53 & 54
Mech replied to Sha35297's topic in Yamaha ATV Forum
It's getting to the stage where we need to be able to connect our laptops to the bikes. I've been doing it for years on cars but bikes are not well supported regarding the addresses we need to query. It will come though, plenty of people picking away at it, and every now and then some helpful bike shop employee borrows the scan tool and downloads some bike specific addresses which often do other models as well. If we can do it, connect to a bike, that's the way to find these problems. A keen man (or woman), with a laptop, can tell more then the half trained parts fitter "technicians" using the factory scan tool.- 20 replies
-
Grizzly 700FI EPS, Intermittent Hard Start, EPS Light on, Codes 53 & 54
Mech replied to Sha35297's topic in Yamaha ATV Forum
Yup, I'd hate that too.. That's even worse than inadvertently curing a problem, but not knowing what it was you did that cured it, or if it's a permanent cure. Second hand unit ? Take the unit out and to a quad shop and ask if they could plug it in and try it on a good bike ? All the manufacturers say to test every component and the wiring in the case of a suspect ecu, then if nothing is wrong, try a known good unit or swap the suspect one into a good vehicle. Not so handy for guys like you and I..- 20 replies
-
The fuel pump will have a hole in it's diaphragm I'd think. The hole may only show up when the diaphragm is flexed to a certain point. I should have probably clicked earlier that it could be the pump leaking.. seen it before and it fits the symptoms perfectly.. My bad. Good work..
-
2004 Bombardier Outlander 330 How To Remove Stator
Mech replied to rgeiser's topic in Can-Am BRP ATV Forum
It's strange that the ohms are good on the stator and they are putting out voltage. I doubt the windings are the problem. A weak magnet from sitting unused perhaps, or metal filings bridging the magnets or bridging the gap between magnets and stator poles ? I'd have expected both those ohm readings, from the black wire, and the reg's body, to be the same, and probably a little less than a half ohm.. Perhaps try a jumper earth from the black wire and/or reg's body to try it. The reg is regulating, but if it's not earthing properly it will think the voltage is higher than it is by some small amount.. If that doesn't make any difference then one last check would be to put a bulb onto the stator wires.. A bulb will work on AC and it will test there is some amperage coming out.. We're on 230 volts here in NZ and I've used a 100 watt household bulb before to test stators.. they glow fairly brightly. If none of that works then it looks like pulling the motor and having a look is the next step..- 16 replies
-
- outlander 330
- outlander
-
(and 1 more)
Tagged with:
-
Just for the record, the far and away most common cause of uneven tyre wear is worn suspension ball joints or bushes, or steering ball joints.. Bent A arms or chassis are occasionally the cause.
-
2004 Bombardier Outlander 330 How To Remove Stator
Mech replied to rgeiser's topic in Can-Am BRP ATV Forum
That's what being professional is all about, sometimes we have to make some pragmatic decision, such as this one you have here, and in these situations we need to be able to explain and justify our reasoning, decisions, actions and workmanship... Which you can.. Depending on the price, fitting a new regulator is probably the pragmatic thing to do, before pulling the bike to bits possibly for no reason. When we can't be certain, it's better to take the cheapest option first. You did check for a bad earth on the reg did you ? And the wire from the reg to the battery ? Either of those could cause the low voltage.. the earth being the most likely..- 16 replies
-
- outlander 330
- outlander
-
(and 1 more)
Tagged with:
-
2004 Bombardier Outlander 330 How To Remove Stator
Mech replied to rgeiser's topic in Can-Am BRP ATV Forum
It looks to me like the reg isn't doing it's job properly. With those voltages at the stator it looks like it should be charging. I wouldn't worry too much about the voltage being slightly low at idle. I'd check the DC output of the reg for any AC, which indicates one failed diode. Then I'd check the earth connection from the reg all the way to the battery, so reg to body, body to battery, and I'd check the charging wire going from the reg to the battery.- 16 replies
-
- outlander 330
- outlander
-
(and 1 more)
Tagged with:
-
Ha.. funny story about the guy frying his belt.. There was a guy in here called Guy a while back bad mouthing the aftermarket belt/pulley system he'd bought and not been able to set up himself.. He reckoned he was frying belts one after another.. He though didn't know what he was doing.. Belt drives are generally pretty reliable it seems these days though. In the rough though, trying to get out of holes or over logs, they really aren't made for it, the owners manuals warn you against doing things like that to your bike.. Belt drives are really only good for cruising around recreationaly. There are more variations of semi-auto or auto than just belt drive though. Some are fully mechanical systems that can take the hard treatment.
-
There's an owners manual in the manual section of this site that tells you how to diagnose a no spark situation. I had a look and I see the wire colours are different to the colours you mention but that's quite common. You will have to figure out which set of wires are which by the numbers of wires there are of each colour, and by their ohm readings. There's no wiring diagram and so it's hard to tell whether the kill and ignition switches should be connected or disconnected for run. I'd leave them attached. The engine is a four stroke and has it's engine oil in the sump and shouldn't need anything else oiling. To check for spark you should take the spark plug out of the bike, fit it to the spark plug lead, and rest the sparking end of the plug on some part of the engine or frame where it will be contacting metal.
-
What makes you think it's a squeal from inside the cases ? Did you find any metal shavings or dust in the cases when you stripped it ? Could it be an engine mount squealing ? Exhaust rubbing ? Something like that.. I'd be really doubtful that anything inside there could be making a squealing, and under throttle, without there being signs of wear, and probably heat.
-
This may be useful... HONDAMATIC CONTINUOUSLY VARIABLE TRANSMISSION INTRODUCTION Automatic transmissions have been used in some All Terrain Vehicles (ATVs) for many years, but until the introduction of the Hondamatic hydraulic transmission, ATV automatic transmissions used a traditional belt drive and pulley system. The fully automatic dual-mode Hondamatic transmission featured on the 2001 Honda Fourtrax Foremanš Rubicon (TRX500) provides these features, and is compact, quiet and extremely reliable for use in agricultural, rural, and recreational applications. The usefulness of the Hondamatic transmission is maximized when combined with the computer-controlled, dual-mode continuously variable change program or the Electric Shift Program (ESP), already in use on the Fourtrax Foreman ES (TRX450ES) and Rancher (TRX350FE/TE) ATVs. The ESP allows the operator to select higher or lower output ratios, providing precise manual control of the Hondamatic transmission. HISTORICAL APPLICATION Soichiro Honda recognized the efficiency and convenience of hydrostatic drives and incorporated the Badalini stepless transmission design into the Juno scooter in 1962. Honda engineers continued to develop their own versions of hydrostatic transmissions and incorporated them into snow blowers, lawn mowers and smaller power equipment. Honda Racing Corporation (HRCš) also applied this technology to the RC250 in 1990-'91. The RC250 was a limited-edition, works-type motocrosser that used the continuously variable transmission to maximize torque output and optimize reduction ratio selection. SYSTEM OVERVIEW In a very simplified description, the Hondamatic hydraulic transmission uses the engine to drive a hydraulic pump that forces hydraulic fluid through sequential pistons. On the other side of these pistons, the pressurized fluid enters a second set of pistons that push against an angled plate (called a swash plate). Because the cylinder body holding the pistons is splined to the output shaft, the pressure exerted on the swash plate causes the cylinder body to rotate. When the angle of the hydraulic motor swash plate is adjusted, the cylinder body (and, therefore, the output shaft) rotates faster or slower, resulting in higher or lower output drive ratios. When either of the two automatic transmission modes (D1-Maximum Performance or D2-Maximum Torque) is selected, the Engine Control Unit (ECU) continuously monitors input from six sensors to position the motor-side swash plate at the optimal ratio. Using the ESP mode, the ECU instructs the control motor to move the hydraulic motor plate to preset angles to simulate specific gear selection. CONSTRUCTION AND OPERATION Operating Principles The Hondamatic transmission is a hydromechanical continuously variable transmission with a fixed-volume piston pump and a variable-volume piston motor in opposition on the same shaft. As the Hondamatic is a closed circuit, any excess hydraulic fluid from the Hondamatic system is recirculated to the transmission using a separate charge pump. The Hondamatic transmission uses standard engine oil as hydraulic fluid. Upon engagement by the centrifugal clutch, the engine turns the transmission's pump-side outer body, causing the fixed-angle pump-side swash plate within to rotate, sequentially stroking the pump side pistons. This action draws low-pressure fluid into the pistons, which discharge high-pressure fluid (corresponding to the input torque). The fluid is distributed to the high-pressure circuit by the distributor valve on the pump side. The distributor valve on the motor side opens and feeds the high-pressure fluid to the pistons on the motor side for the suction stroke. Each distributor valve is eccentrically synchronized to the rotation of its respective swash plate, ensuring that fluid is transferred at the proper time. The amount of fluid discharged depends on the angle of the motor-side swash plate. The greater the slant, the farther the pistons move and the more fluid they transfer. This additional volume transfer makes the motor side less efficient, resulting in a differential based on the volume transferred. As the motor-side pistons travel down the slope of the motor side swash plate, the fluid pressure is drawn through the pistons and rotates the motor-side cylinder body (which houses the pistons). As the cylinder is splined to the output shaft, the output shaft also rotates, transferring power to the drive train. When the motor-side swash plate is perpendicular to the pump axis, the pistons do not stroke (therefore, oil is not discharged). In this condition, oil cannot flow between the pump and the motor and the motor is hydraulically locked (1:1 gear ratio). An overdrive is achieved by adjusting the swash plate to an angle beyond perpendicularity to the pump axis, creating a drive ratio of 1:0.84. As the pistons begin their travel back up the motor-side swash plate, they begin their discharge stroke. The hydraulic fluid is transferred back through the motor-side distributor valve and into the low-pressure circuit of the body. The fluid then passes through the pump-side distributor valve, where it is timed to the suction stroke of the pump pistons. Distributor Valves The hydraulic fluid is transferred between the pump and motor piston chambers by the sprue-type distributor valves arranged radially around the shaft. The pump-side and motor-side distributor valves are eccentrically arranged on the shaft and are aligned to time the transfer of low-pressure and high-pressure fluid in tune with the direction and inclination of the pump and motor swash plates. As the cylinder rotates, the eccentrically arranged valves slide in and out of the cylinder body, opening and closing the paths in the body. Compression Braking and Pressure Control During normal running, the check valve in the pump-side cylinder feeds hydraulic fluid into the low-pressure circuit. The check valve is open when the hydraulic pressure in the low-pressure circuit drops below a specified level and, upon achieving the proper pressure, closes to prevent backflow. Under engine compression braking conditions (where the rotational force comes from the wheels), the motor side becomes a pump (driven by the input shaft) and the pump side becomes an hydraulic motor. In this situation, the high- and low-pressure circuits in the Hondamatic body are reversed. The Hondamatic transmission uses a separate check valve to feed hydraulic fluid to the engine braking low-pressure circuit. Pressure control valves vent excessive high-pressure fluid into the low-pressure circuit during both normal running and compression braking conditions. CHECK VALVES AND PRESSURE CONTROL VALVES Torque Amplification The input reaction force torque from the engine is transmitted to the pistons that are fixed within the rotating cylinder. This force is then transferred through the cylinder to the shaft (mechanical power train). When the ratio is 1:1 and the motor side swash plate exerts no reactive force against the motor cylinder, the input torque is transferred directly to output torque with no amplification. When the angle of the swash plate is increased, the reaction force increases, amplifying the output torque. The total output torque is the sum of the input reaction force torque and hydraulic output torque. Shift Mechanism As previously discussed, the output shaft speed is controlled by the angle of the motor-side swash plate. The position of this swash plate is determined by the ECU, which uses various pieces of information to send commands to the control motor that moves the swash plate arm. The signals used to determine optimal Hondamatic output are: Throttle opening (throttle sensor) Vehicle velocity (speed sensor) Engine speed (rpm) (ignition pulse generator) Hondamatic motor-swash-plate angle (angle sensor) Gear position (gear position switch) Control mode and map (mode/map switch) In the fully automatic modes (non-ESP), the ECU is continuously monitoring these signals. When a change in motor swash plate is deemed necessary, the ECU sends a signal to the control motor, which moves the ball screw (attached to the swash plate arm) via reduction gears. There are two rider-selectable automatic modes: D1-Maximum Performance and D2-Maximum Torque. The D1 mode emphasizes higher engine horsepower output for riding performance, while the D2 mode maximizes torque output performance. Within these rider-selectable modes, there is a choice of standard output ratios (Drive) or lower output ratios (Low) using the automobile-like shift lever. Reverse can also be selected using this gear lever which engages a reverse gear located in the subtransmission. When the operator selects the ESP feature, the UP and DOWN buttons on the handlebar switch are enabled. When the appropriate button is pressed, the ECU commands the control motor to move the swash plate to the next higher or lower preset position. SUMMARY The Hondamatic transmission is the first continuously variable transmission of its kind. Housed within a compact, fully sealed assembly, it uses the principles of hydrostatic drive, mechanical power transfer and modern electronic controls to create a unique hydromechanic drive. Unlike traditional belt drives, the Hondamatic is quiet, maintenance-free, rugged, impervious to external contaminants and features true engine braking. Test Ride | Features | Specifications Top Of Page | Honda Index | New Models | Home Copyright © 2000 by Motorsports Network. All Rights Reserved.
-
Heck yeah Jim, good tools are a must.. My workshop equipment is really simple, but all good quality gear.
-
There are quite a few types of quad transmissions these days, manual shift box, electric shift box, Twin disc/clutch electric/automatic shift box, automatic/electric shift box, and belt drive CVT. I prefer the old manual shift myself, for simplicity of service and operation, and for the solid drive. Automatic are never as good at controlling the vehicle when the going gets really tough.. not in bikes or vehicles.
-
2000 Suzuki Quadmaster 500. Runs for 15 mins, stops - Oil in air filter
Mech replied to MMC's topic in Suzuki ATV Forum
As has been suggested, it might be a tight valve causing it to stop after it gets fully warmed up, or it could have fuel in the oil, which would account for the dirty filter and the behavior after it gets warmed up. The fuel could be evaporating out of the oil once it's warm, flooding the engine and dirtying the filter. -
You guys don't need any more bikes..
-
Ha... those are pretty extreme alright... Nice !