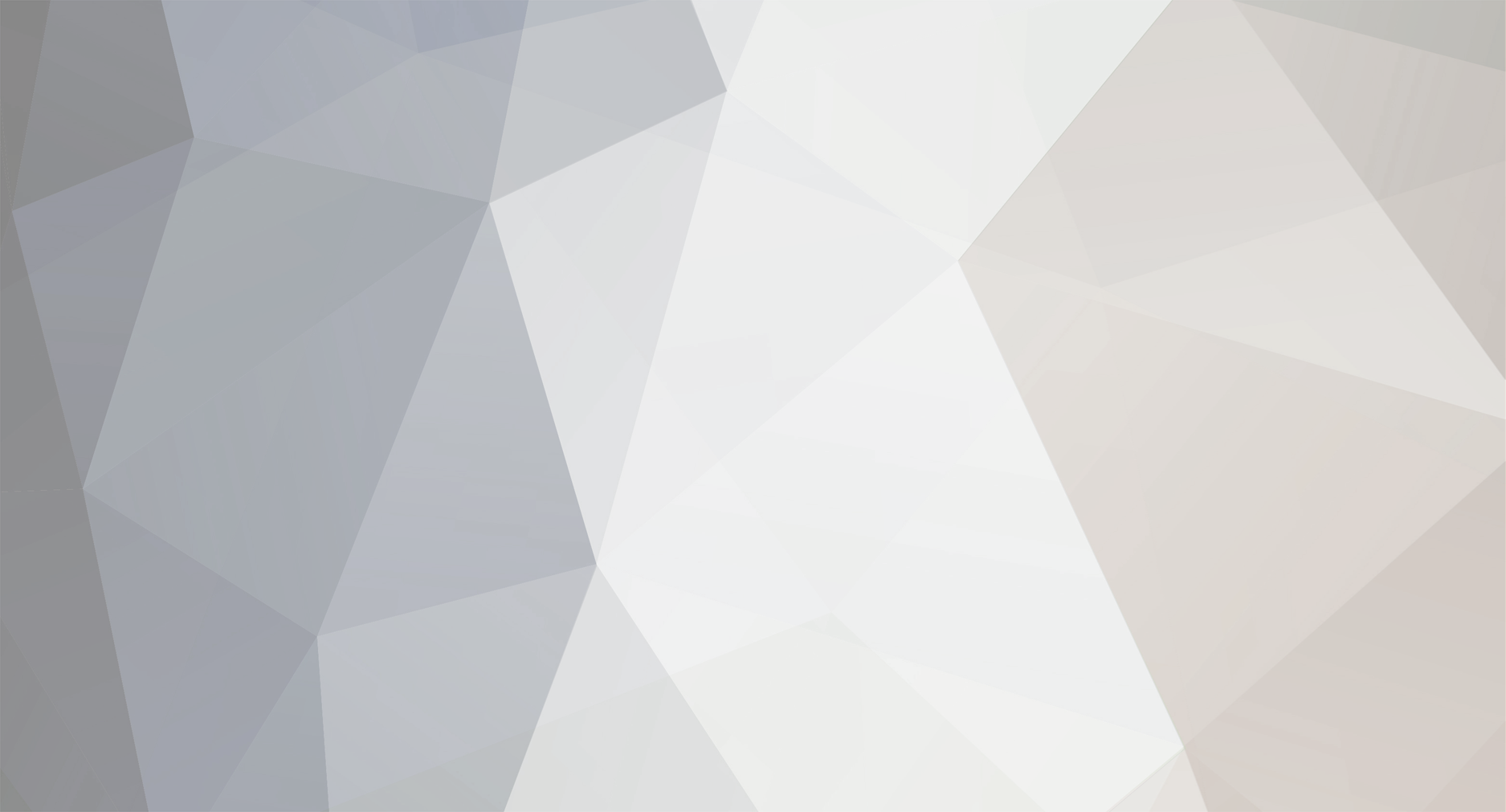
Mech
Premium Members-
Posts
3,955 -
Joined
-
Last visited
-
Days Won
264
Content Type
Profiles
Forum
Gallery
ATV Magazine
Events Calendar
Downloads
Store
Community Map
Everything posted by Mech
-
Look the parts up on an online parts place like partzilla and they will likely have some way or where, that they will tell you what else that parts fits. https://www.partzilla.com/product/yamaha/5GH-17660-00-00?ref=a5a2e51fd1b12c786666c251d29374489d129825 At the top of that listing click on the button called "clutch" and it will take you back to a parts diagram where you can check each part..
-
Haha.. People like to complicate things.. You're very welcome Kuba. I'm always happy to help anyone that's trying to help themselves.
-
No, valves should not need adjusting every year. The most common reason they need readjusting is because they weren't set to the right setting to start with. If you are adjusting them with feeler gauges you need to be sure there is no wear on the valve end or the rocker that's upsetting the measurement. It might be better to use a dial gauge that measures in thou, or calculate how much of a turn it will take of the screw to give the right gap, and then back the screw out from zero gap to get the required gap. It's important that you end up with as much clearance as possible, without noise, hot or cold. Some old bikes with worn rockers and valves need a bit of trial and error to get them adjusted and stable. The apparent gap isn't always the only play. Sometimes we need them to have a slightly bigger than recommended gap, and sometimes slightly less. First up check the gap cold and then hot and see whether they gain or loose clearance when they warm up. Then factor that in as you are calculating/adjusting the clearance. Always start with a little too much gap, and then if they are noisy, reduce it till they are just quiet hot and cold and then they should be stable.
-
It will be a metric size, and a whole figure, no fractions. Use a ruler. 10, 12, 14, 16 are all common sizes.. And.. you can buy allen key tools that fit onto ratchets or power bars.. I'd recommend you get one of those. They use them on other stuff that gets done up a lot tighter than that bung, so the power bar option. might be useful in the future.
-
It's what they call a bullet connector. One wire has a bullet head shaped terminal and the other has a tube terminal.
-
The book I've been working from latterly, the one which seems to be the best for your bike(as far as I can tell), says the pick up coil should be measured at the engine connector and it should have 459-561Ohms, but I'd check that figure at the cdi to check the wiring as well. Not all pick up/trigger coils put out voltage, some just change resistance as the flywheel tag goes past.. If it's one of those sort it should have some very small voltage and current coming out of the cdi..
-
Welcome along Clem. Manuals are over that way... Coffee's here. I think there are some beers in the fridge..
-
If that's all the metal in there then it's a good one .. haha. See in the picture of the slippers on page two it looks like those bits of rubber could have come off the outer edge of the fixed slipper, and it could have happened just as the chain came off.. especially if the bits were laying there under the slipper and hadn't been washed away by the oil..
-
It's not really rubber. The straight one that's on the tight side of the chain is really just to stop the chain from getting into a rhythm that causes it to flutter and twitch like a fan belt does at certain revs. It hardly touches the chain.
-
That second one goes up to a "T", which fits into a slot in the top of the barrel, under the head. You have to take the head off to get that out. I wouldn't necessarily say that the slippers need replacing just because of those two strips of rubber. They sometimes have bits of excess rubber hanging over the sides of the steel backing that can get worn through and drop off like that. I've seen it before. First up, is the one you got out damaged ? Is the rubber worn thin in the middle of it's length ? Are there grooves where the chain's worn ? Then, I'd try looking down from the top at the fitted one, with a light at the top or bottom, and look for deep grooves where the chain links wear, or bare metal showing on the slipper, or chunks lifting off the steel backing. If those strips had torn/lifted off where the chain rubs, there would be more of it, those wouldn't be the only bits and there'd be lots of rubber chips and mess. Look for the sort of wear and tear that would be expected if the slipper had worn right down to the self destruct point.. I'd check the chain for wear and consider replacing that, and the tensioner, but honestly, I've fitted lots of chains without changing those slippers.
-
Glad you got it sorted. Well done. Perseverance always wins, giving up never does. Always take things apart very carefully Valkman, and lay them out in order and direction of removal, that is, lay all the inner sides(or outer) downwards on the bench, and in their order. It's never a good idea to just "rip things apart"(not saying you did), because we overlook indications of what went wrong(for one thing), and we too easily forget which way they came apart. Take every part off one at a time, inspect it, and lay it out carefully..
-
Yup, it's the theoretical diameter of the outside of the threads. Once you get the file you will be able to figure the pitch, which is the mm distance between threads. That will be about 1.25mm probably. Good manuals eh ?
-
And seriously, those rattle guns are not good for working on things.. Nuts and bolts need to be turned slowly, especially while they are still tight, but even after they are loosened off, if you try to wind a nut down long threads too fast, even by hand, they will get tight..
-
Oh ok, sorry to hear about the eyes. Mine aren't what they used to be either.. Get a thread file for metric threads, they are cheap and come with eight different pitches on each one. You hold them near the thread and look(squint) to figure which one fits best..haha. Then you just gently rub them up and down over the old threads at the right angle for left hand threads.. turning the shaft or rocking the file as you go..
-
Ok.. Wires are described by their main colour and then the stripe, so white wire with a red stripe is W/R, lines that cross with a small dot on the intersection are connected, intersections without a dot are not joined, things that have a dotted box around then are all one unit or part, we can tell if they have a wire tail or if the wiring plug goes straight into the unit by the relationship between the dotted line and the joins/plugs. I'd suggest printing the whole wiring diagram and then using coloured pencils to colour wires in as you trace and confirm them.. I suspect that your bike might have the wrong switch somewhere, either the kill or the main, or possibly both. I'd look at the plugs on the ends of the wiring loom and check the shape and wire colors and ignore the switches for a while.. Figure which wiring loom you have, and then diagnosing the wrong switch or short or whatever should be much easier.
-
I'd get a thread file first and try cleaning that thread up. The thread file will tell you what the pitch is, Hopefully the threads will come right and a new genuine nut will do. if you need to find a nut,you will have to make an educated guess what size it is by measuring the diameter. It will be a metric diameter and although most metric threads are whole mm steps you can get special threads in half mill, so measure carefully. You won't get a left hand thread in any common tap and die set, but they can be bought quite easily individually if you really need one. If the tread file won't clean up the threads though then neither will a die nut. And yeah, zap guns are hard on threads always and shouldn't be used for routine undoing stuff. They spin too fast and promote galling even in good threads.
-
I think Kuba that you need to check the bikes wiring to see what sort of kill switch system it's meant to have, earthing or switching power off, Those seem to be the two common systems. Then you need to check withing that main divide what sort of main switch system it uses, and then get the right switch for there.. I think that will get you to the problem..
-
Yeah, we can inspect the chain for wear, and the slippers, and be pretty certain whether they are ok or not. The tensioner is the tricky bit. And that backfiring throwing the chain or timing belt is well known. Some motors they warn you against rotating backwards because the belt can jump.
-
I looked in a lot of diagrams for all sorts of models and years and none of them had a switchable red coming out of the main/key switch.. They all only had red going in, some one red and some two.
-
Check the ratcheting mechanism on the tensioner really carefully.. If a motor backfires or bounces backwards as it's coming to a stop, the tension comes on the wrong side of the chain and can subject the tensioner to pressures it wasn't designed to take.. A defective ratchet can fail under those conditions..
-
If someone had swapped the main switch it could cause some confusion..
-
Here are the other two I have... 00-05bigbear-kodiak400.pdf 99ymf400f.pdf
-
I've got three different versions, and they all claim to cover that year kodiak, and two of them say they also do big bears for the same years.. Different markets though, even if they are the same model, can have different components.. local product.. There are several different main switches, and several different kill switches, and I think some switches can be used in different wiring configurations.
-
This is supposedly the right diagram.. There is a red from the stator to the cdi. 93-05Kodiak400.pdf
-
Dang.. Gw's right.. You will have to pull the right side case off P5200.. I'd been thinking the chain was on the left..